はんだ付けのご依頼を企業様から以前いただきましたので、その内容をご紹介いたします。
「チップ抵抗」と「チップLED」、そして「表面実装コネクタ」の3種類をはんだ付けしますので、それぞれの様子を前編・中編・後編と3つに分けてご覧いただきます。
この記事は、後編になります。
- 前編:チップ抵抗
- 中編:チップLED
- 後編:表面実装コネクタ
前編と中編をご覧になられていない方は、まずは前編と中編をご視聴下さい。
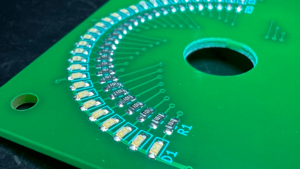
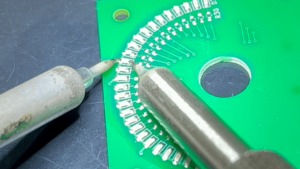
今回、表面実装のコネクタをはんだ付けしていきますが、はんだ付けする部品は基板1枚に対してコネクタ1個です。
- 前編では、チップ抵抗が基板1枚あたり30個。
- 中編では、チップLEDが基板1枚あたり30個。
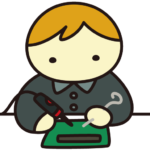
とにかく数が多く大変だったよ
はんだ付けをやれどもやれども一向に数が減りませんでしたからね(笑)
でも今回は、基板一枚に対して、コネクタ1個です。
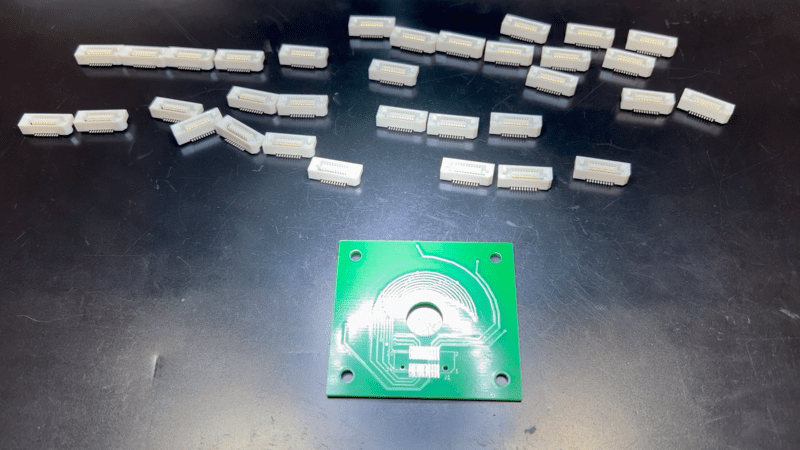
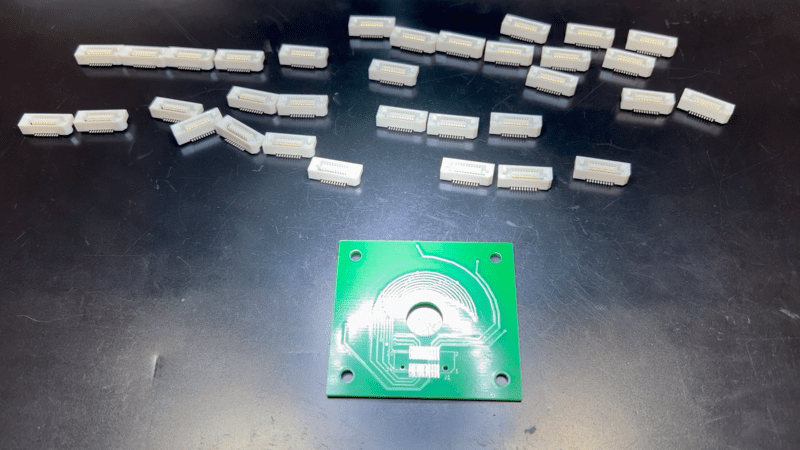
基板が100枚でコネクタが100個なので、気分的にはかなり楽になりました^^
ただし、気は抜けません。
はんだ付けする際に注意しなくてはいけない点がいくつかありますので、その辺りも解説しながら進めていきたいと思います。
表面実装のコネクタをはんだ付けする注意点
表面実装コネクタをはんだ付けする際の注意点について解説していきたいと思います。
このタイプのコネクタは、基板と基板の接続に用いられることが多いと思います。
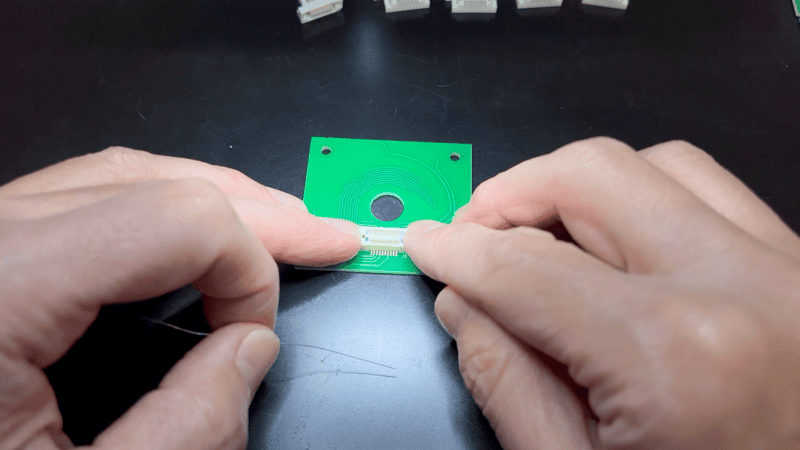
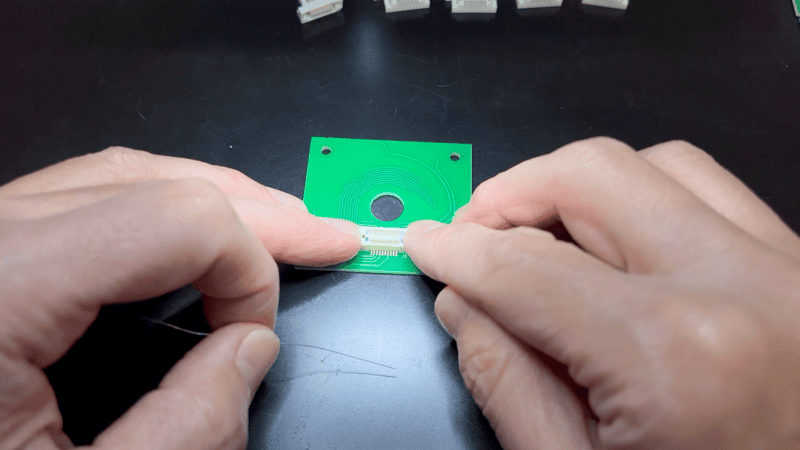
コネクタだけで勘合しますので、コネクタの実装位置が重要です。
曲がってはんだ付けしてしまったり、浮かせてはんだ付けしてしまったりすると、勘合する際にコネクタに大きな負荷がかかってしまいます。
なので、はんだ付けする位置には、細心の注意を払わなくてはいけません。
ですが、今回使用するコネクタには、位置決めのボスがついており、基板にもボス用に穴が空いていますので、大きな位置ズレは大丈夫でしょう。
ただ、基板によって遊びが大きいものもありますので、位置決めボスに頼り過ぎるのも駄目ですね。
また、方向にも注意が必要です!
コネクタを逆に実装してしまうと、修正が非常に困難です。
外すことが出来たとしても、コネクタを損傷させてしまう事が多いので、間違わないようにしなくてはいけません。
ですが、位置決めボスがある場合は、大丈夫なんです!
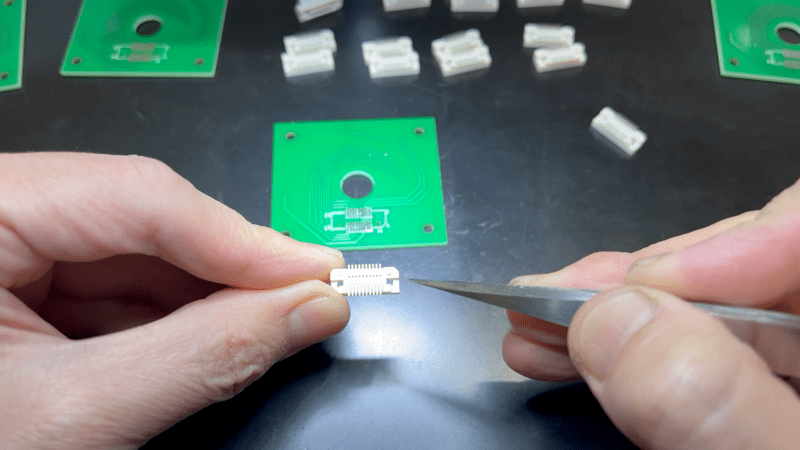
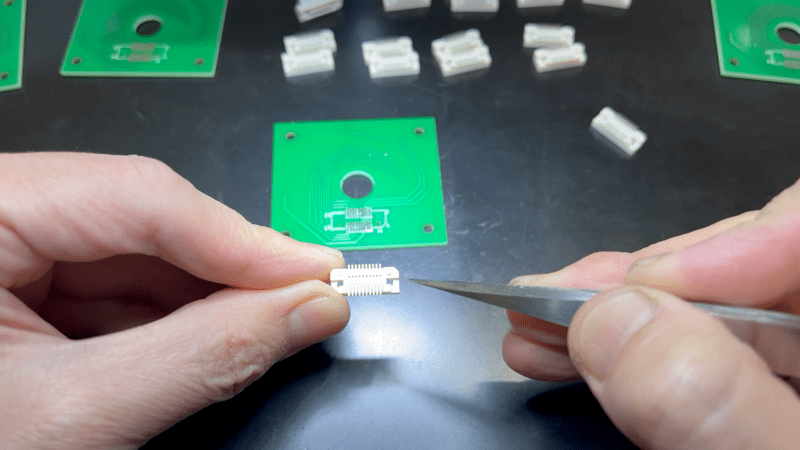
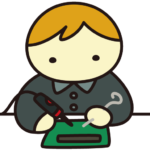
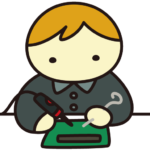
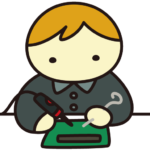
位置決めボスの大きさが、大きいものと小さいものになっていて、逆には入らないようになっているので安心なんだよ。
注意点を書き出すとキリがないのですが、もう一点、解説しておきます。
それは、はんだブリッジです。
コネクタを乗せる前の基板を見ていただくと、パットがコネクタの下部まで伸びてきているのがお分かりいただけるかと思います。
結構パットが長く、コネクタの下部まできているので、コネクタの下ではんだブリッジしてしまうと大変です。
器用な方であれば簡単にはんだ修正出来るかと思いますが、不慣れな方だと修正に苦戦するかと思います。
そもそも、コネクタの下部ではんだブリッジすると、不良を見つけにくいという問題もあります。
なので、はんだ付けする際には、はんだブリッジには十分気を付けてはんだ付けする必要があります。
表面実装のコネクタをはんだ付けする注意点は、以上となります。
表面実装コネクタのはんだ付け
いよいよ表面実装コネクタのはんだ付けです!
下記のような流れで、はんだ付けを行なっていきます。
- パットにフラックスを塗布する。
- コネクタを乗せ、仮止めする。
- コネクタのリードにフラックスを塗布する。
- はんだ付けする。
では、流れに沿って進めながら解説していきますね。
パットにフラックスを塗布していきます。
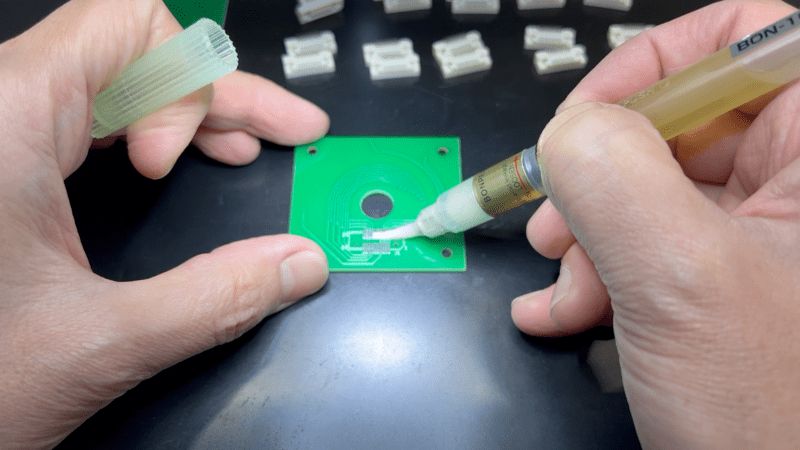
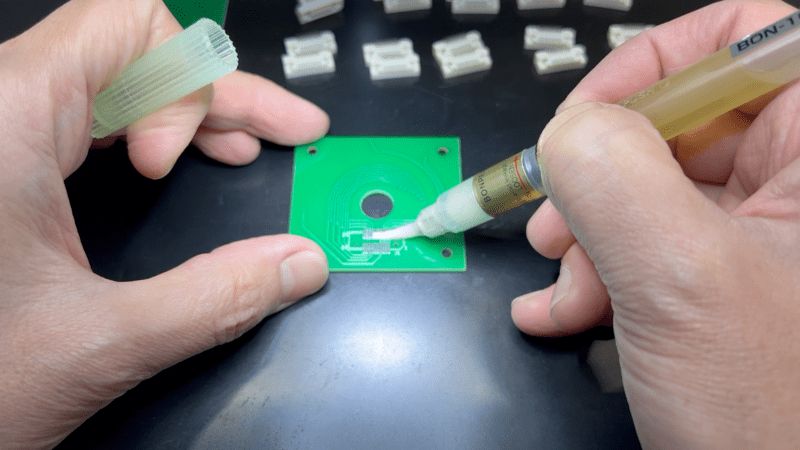
チップ抵抗とチップLEDをはんだ付けした時と同様に、20枚ほどまとめて進めますので、一度にフラックスを塗布していきます。
パットにフラックスを塗布する理由ですが、コネクタを乗せるとパットが隠れてしまいます。
そうすると、コネクタのリード裏側にハンダが流れにくくなりますので、リード裏側にハンダが流れやすく馴染みやすいようにフラックスを先に塗布しておきます。
コネクタを乗せ、仮固定を行っていきます。
いくつか注意点で解説した通り、位置決めボスが大小になっており、コネクタは入る方向にしか入りませんので、まずはすべてのコネクタを基板に乗せます。
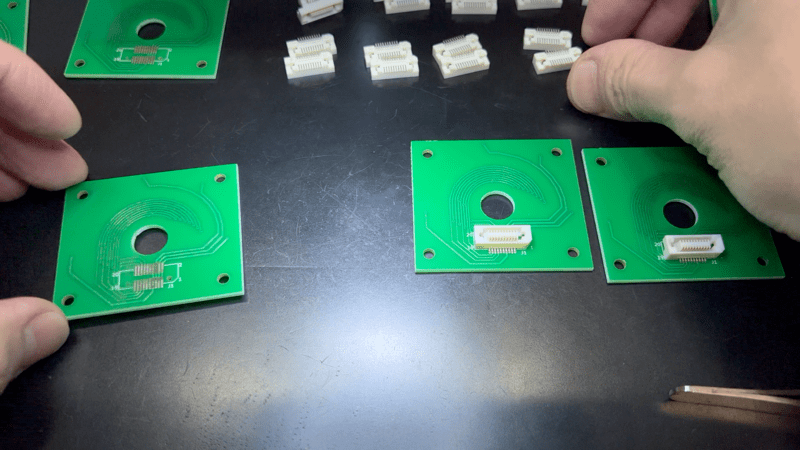
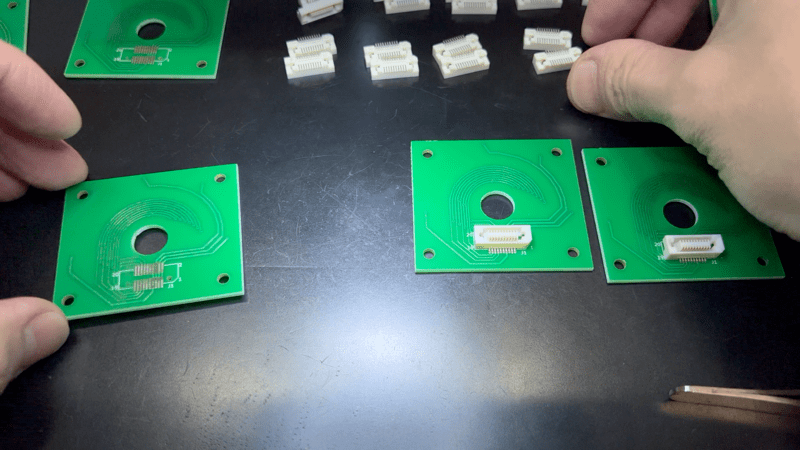
次に、仮固定です。
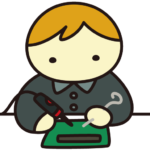
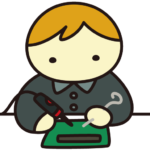
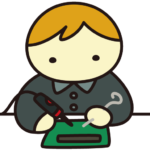
ここが一番重要なんだよね〜
少し遊びがありますので、出来るだけパットの中央にコネクタのリードが乗るように仮固定します。
この仮固定でズレてしまうと、いくら綺麗にはんだ付けしてもコネクタはズレたままになるので、注意して仮固定を行います。
また、浮きにも注意する必要があります。
現場では稀にある事なのですが、機械ではんだ付けされた場合でもコネクタが浮いている事ってあるんですよね(笑)
部品の購入先にもよるかと思うのですが、実は、購入した部品でも初めから、コネクタのリード(足)が曲がっていることがあるんです。
このリードが曲がっている方向が下方向に曲がっていたりすると、そのリードの影響で、コネクタ全体が浮き上がってしまいます。
曲がりが酷いと、他のリードがパットから離れ、ハンダが付いていない状態になってしまうこともあるんですよね^^;
なので、仮固定の際には、コネクタが浮いていないかどうかにも注意を払う必要があります。
コネクタのリードにフラックスを塗布していきます。
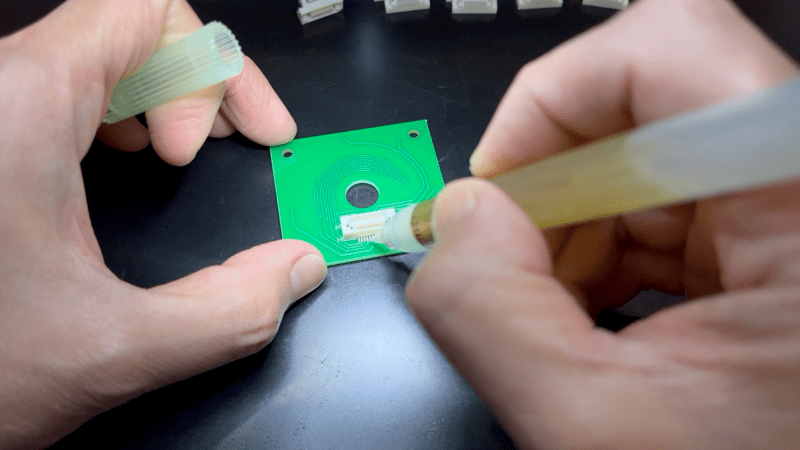
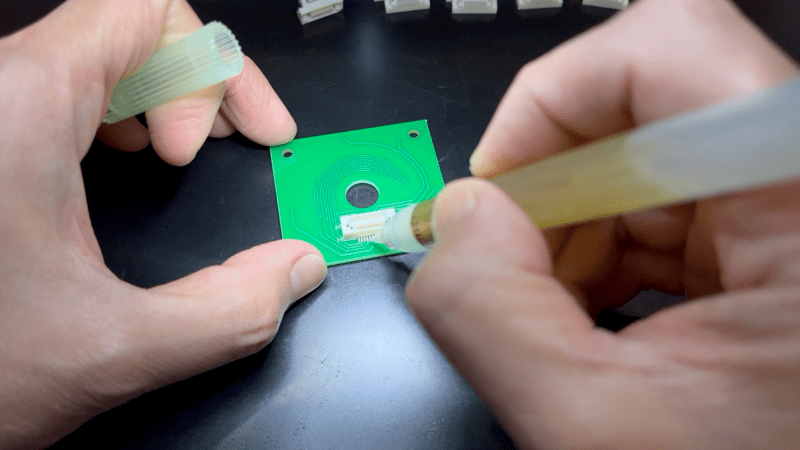
このフラックスは、コネクタのリードにハンダを馴染ませやすくするのと、はんだブリッジを軽減させる為に行います。
ただし、フラックスを塗布する際に、コネクタの勘合部分には絶対にフラックスが入らないように注意しなければいけません。
理由は、接触不良の原因になるからです。
コネクタのはんだ付けを行っていきます。
今回は、大きめの先端がカットされたコテ先を使ってはんだ付けをしてみました。
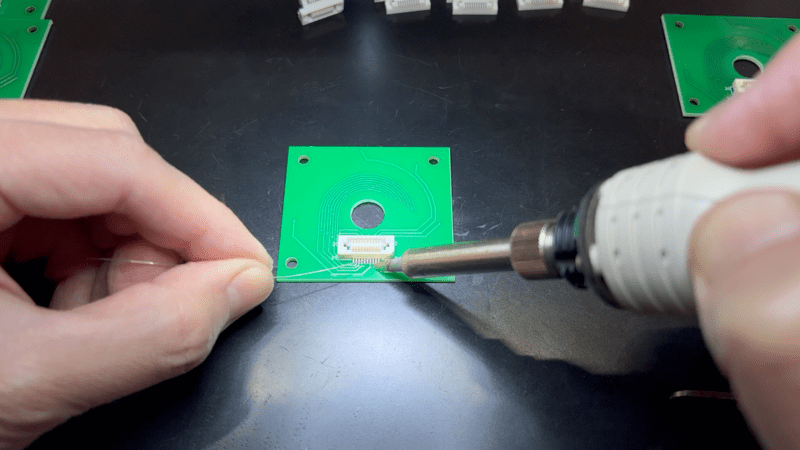
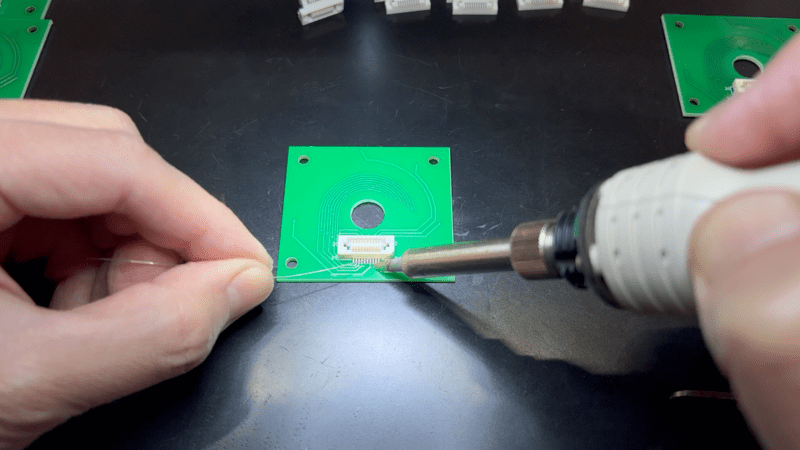
早く終わらせる必要がありましたので、はんだ付けは、「引はんだ」や「流しはんだ」と言われる手法で行っています。
このはんだ付け方法は、QFPなど隣接する多くのリードがある部品をはんだ付けする際によく用いられます。
慣れない方が行うと、リードを曲げてしまったり、パターンを断線させてしまったり、パットを剥がしてしまったりする危険がありますので、もし参考にされる場合は、練習をしてから行うようにしてください。
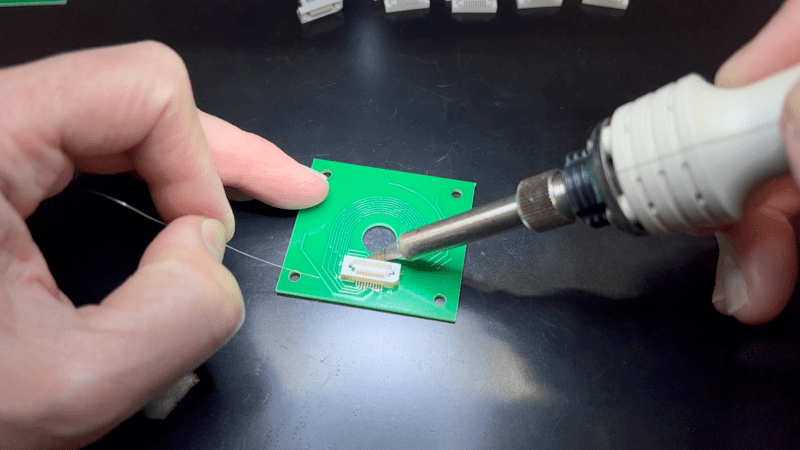
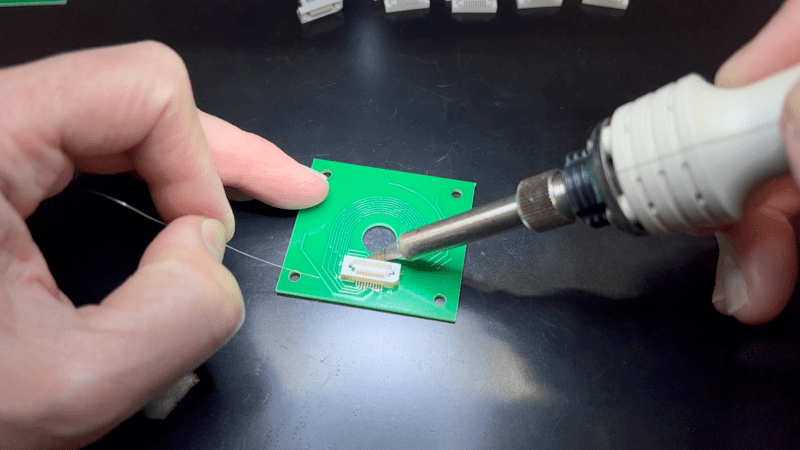
ここでお詫びしないといけないのですが、コネクタのはんだ付けしている部分を撮影したかったのですが、コネクタの死角になってしまって見にくかったり、コテ先の死角になってしまって見にくかったりと、肝心な所が非常に見づらい画像になっております。
普段から、出来るだけ作業者目線での画像を撮るように心がけているのですが、うまく撮影することができませんでした。
将来的には、今使用している実体顕微鏡が三眼式なので、顕微鏡で作業中の様子を録画できるような、顕微鏡用カメラを導入したいと考えています。
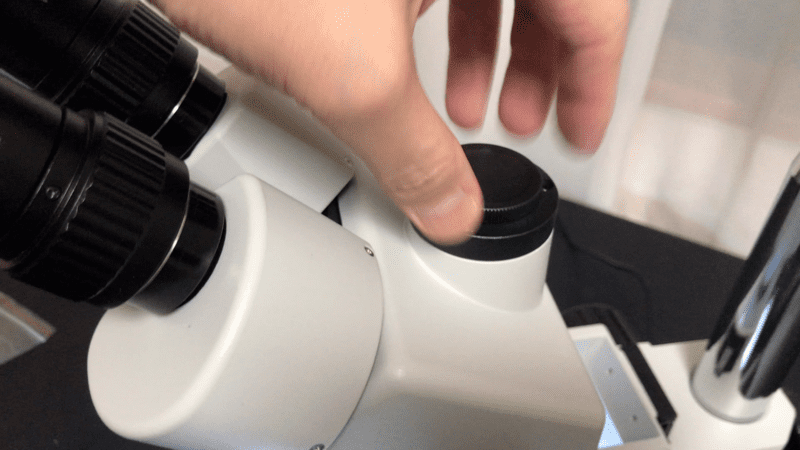
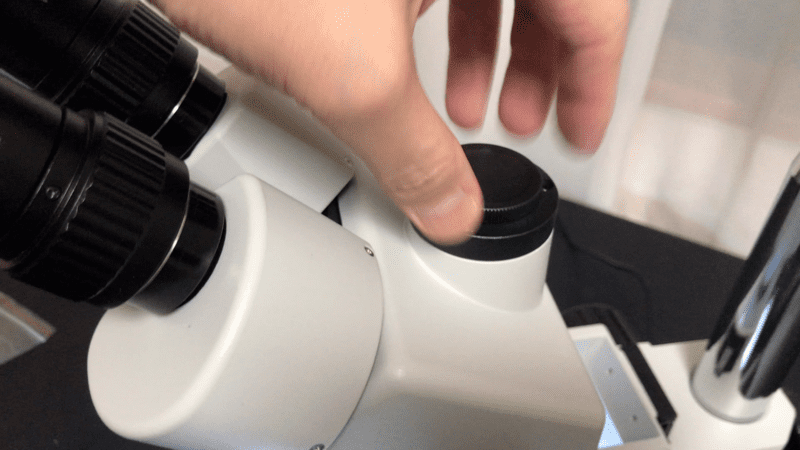
もし、視聴者様で私が使っている「SWIFTのS7-TP520-EA10-56」に適しているオススメのカメラをご存知の方がいらっしゃいましたら、コメントでお教えいただけるとありがたいです!
まとめ
表面実装コネクタのはんだ付けの様子をご覧いただきましたが、如何だったでしょうか?
「引きはんだ」や「流しはんだ」というはんだ付け方法を初めてご覧になられた方もいらっしゃるかと思いますが、こんなはんだ付け方法もあるんですよね。
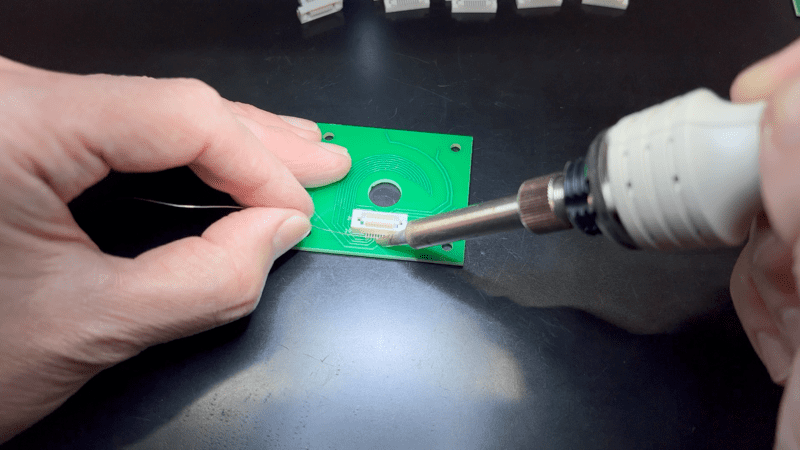
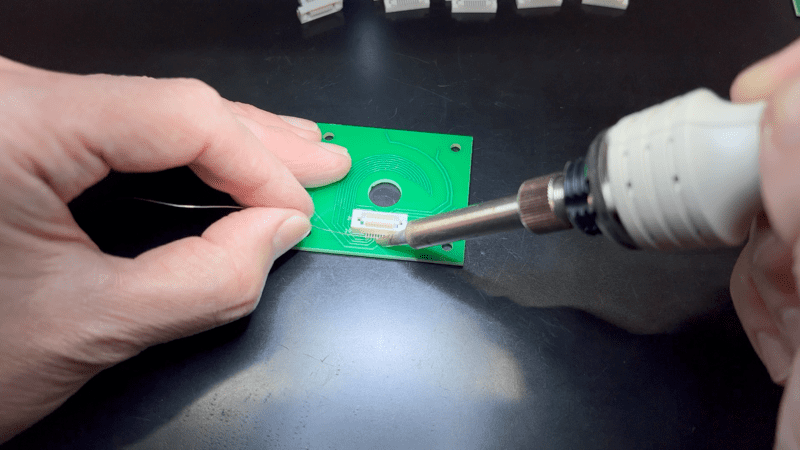
DIYで表面実装のコネクタをはんだ付けする機会は少ないかと思いますが、隣接する多くのリードがある部品をはんだ付けする際には有効な方法なので、練習基板などで挑戦するのも面白いんじゃないかなと思います!
今回は、はんだ付け方法以外にも、表面実装コネクタをはんだ付けする際に注意しなくてはいけないポイントをいくつかご紹介させていただきましたね。
まずは、
コネクタ同士を嵌合することが多いので、負荷がかからないよう、コネクタをズレてはんだ付けしたり、浮いた状態ではんだ付けしないように注意する事を解説しました。
次に、
コネクタの下部ではんだブリッジすることがあり、ハンダ不良を見つけづらいので、はんだ付けする際には注意しましょうと解説しました。
あと、フラックスを塗る際には、コネクタの嵌合部分にフラックスが入らないようにという事も言いましたよね。
理由は、コネクタが接触不良になる可能性が大きいからです。
これは、洗浄にも関係します。
今回は表面実装コネクタの洗浄を行いませんでした。
というのも、コネクタを洗浄することによって、フラックスの残差がコネクタの端子部に残り接触不良を発生させるリスクがあるからです。
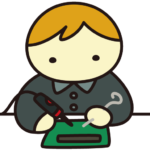
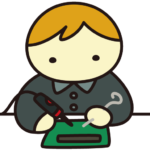
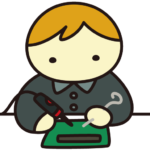
基板枚数が多いと、IPAなどに基板を浸して洗浄するので、コネクタの端子部にフラックスの残渣が残るリスクがあるんだよね。
そのため、使用しているフラックスも無洗浄タイプを使用しており、洗浄をしなくても大丈夫な状態で行っていました。
こういう事もありますので、接点が存在するような部品を洗浄する際には、接触不良を発生させてしまう可能性があることだけは、覚えていた方が良いかと思います。
以上で、今回ご依頼いただいたはんだ付け作業は全て終了となります。
コメント